Unveiling the Essential Role of Rotary Aviation Apex Seals in Engine Performance Enhancement
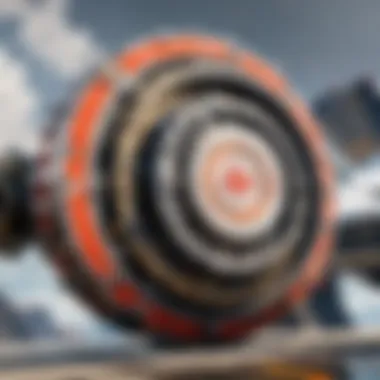
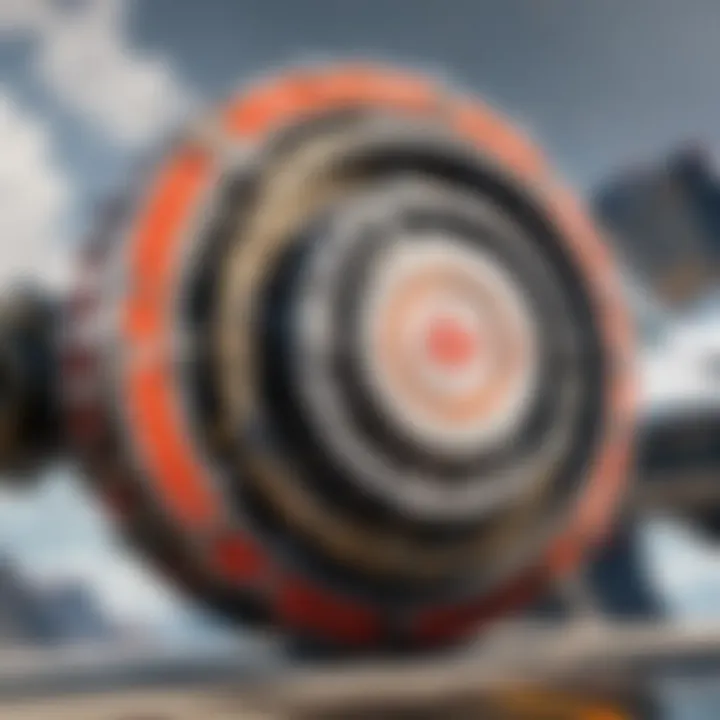
Game Updates and Patch Notes
Embarking on an exploration of the intricate workings of rotary aviation apex seals is akin to deciphering the heartbeat of engine performance in rotary aircraft. The apex seals, crucial components nestled within the engine's core, wield a profound influence on elevating operational efficiency and reliability. By delving into their design intricacies, material composition nuances, and indispensable maintenance practices, we unveil the essence of these seals in enhancing rotary aircraft prowess.
Character Guides
Surveying the realm of rotary aviation apex seals opens vistas to a profound appreciation for the artistry imbued within their construction. Each seal epitomizes meticulous engineering, embodying a balance of durability, flexibility, and resilience. Understanding their deployment within the context of rotary aircraft illuminates their indispensable role in fortifying engine endurance and optimizing performance. The synergy between design precision, material selection, and proactive maintenance underpins the seamless operation of these seals, heralding a new era of sustained efficiency and reliability.
Weapon Analysis and Loadout Suggestions
Diving into the realm of rotary aviation apex seals, we unravel a tapestry of precision and purpose that defines their overarching impact on engine functionality. Analogous to the choice of weapons in a player's arsenal, the selection and configuration of these seals significantly dictate the operational efficacy of rotary aircraft. Analyzing their composition, tolerances, and operational parameters sheds light on their harmonious integration within the engine matrix, akin to assembling the ideal weaponry loadout for optimized performance. The strategic alignment of rotary aviation apex seals serves as a linchpin in navigating the skies with unparalleled efficiency and resilience.
Game Strategies and Tips
As pilots steer the course of rotary aircraft through jagged terrains and dynamic environments, the importance of rotary aviation apex seals resonates as a beacon of reliability amid unpredictable challenges. Unveiling a trove of strategies and best practices for optimizing engine performance through vigilant seal maintenance lays the foundation for elevating operational prowess. Implementing proactive measures, aligning with recommended maintenance schedules, and leveraging insights from industry experts culminate in a dynamic gameplay approach that ensures peak engine efficiency and unwavering reliability amidst the turbulence of flight.
Introduction to Rotary Aviation Apex Seals
Rotary Aviation Apex Seals play a pivotal role in optimizing engine performance within the realm of rotary aircraft. These seals are the unsung heroes working tirelessly behind the scenes to ensure the smooth operation and efficiency of rotary engines. Understanding the basics of these seals is crucial for anyone seeking to grasp the intricate mechanisms that drive rotary aircraft engines towards peak performance. Delving into the design, materials, and maintenance of these seals illuminates their profound impact on the overall efficiency and reliability of rotary aviation.
Understanding the Basics of Rotary Aircraft Engines
Fundamentals of Rotary Engine Operation
In the intricate world of rotary engines, the fundamentals of engine operation serve as the foundation upon which optimal performance is built. These fundamental aspects dictate how rotary engines function, emphasizing aspects like combustion cycles, rotor configurations, and power delivery mechanisms. Understanding the nuances of rotary engine operation is paramount in comprehending the critical role that apex seals play in sustaining engine efficiency and reliability. The unique design of rotary engines sets them apart in the world of aviation, offering advantages such as compact size and high power-to-weight ratios.

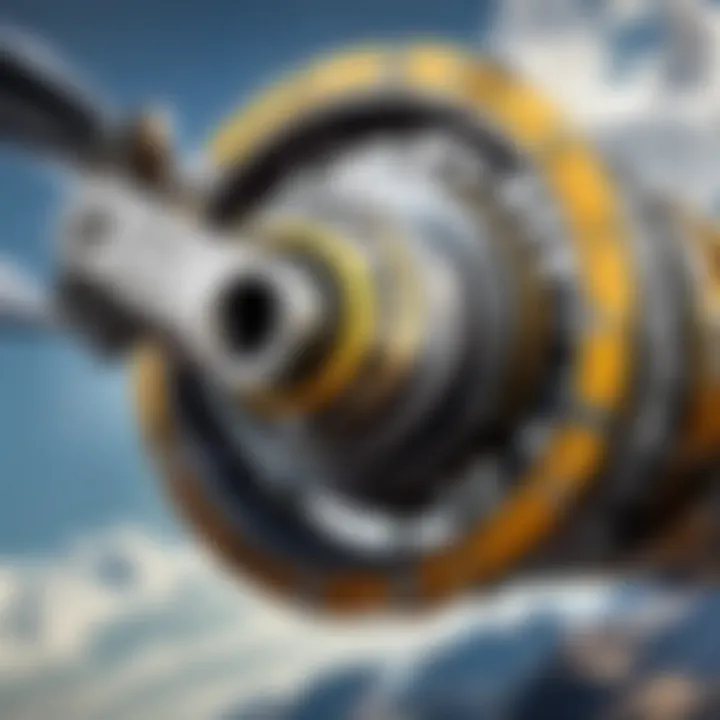
Importance of Apex Seals in Rotary Engines
Apex seals stand as essential components within rotary engines, serving as the primary interface for maintaining compression, facilitating efficient combustion, and ensuring optimal power output. These seals play a vital role in sealing the combustion chamber, thereby preventing gas leakage and maximizing engine efficiency. The design and functionality of apex seals significantly impact the overall performance of rotary engines, highlighting the importance of selecting high-quality materials and precision engineering techniques to enhance durability and performance.
Evolution of Apex Seals in Rotary Aviation
Historical Perspectives
The evolution of apex seals in rotary aviation traces back to the early days of rotary engines, where basic seal designs laid the groundwork for modern advancements. Historical perspectives provide insights into the challenges faced by early seal configurations, leading to iterative improvements that enhance seal longevity and efficiency. Over time, technological advancements have revolutionized apex seal materials and geometries, ushering in a new era of performance and reliability in rotary aviation.
Technological Advancements
Technological advancements in apex seal design have revolutionized the performance capabilities of rotary engines, introducing high-temperature alloys and carbon-based composites to enhance durability and efficiency. These advancements have enabled manufacturers to push the boundaries of engine output and reliability, setting new standards for rotary aviation performance. The integration of advanced materials and manufacturing techniques has paved the way for greater innovation in apex seal technology, ensuring continuous improvements in engine performance and longevity.
Challenges Faced by Rotary Aviation Apex Seals
Heat and Pressure Resistance
One of the primary challenges encountered by rotary aviation apex seals is the demand for exceptional heat and pressure resistance. As these seals operate within high-temperature environments and endure intense combustion pressures, maintaining structural integrity and sealing effectiveness is paramount. Heat and pressure resistance properties play a critical role in the longevity and performance of apex seals, requiring advanced materials and precision engineering to withstand the harsh operating conditions experienced in rotary engines.
Wear and Tear Issues
Wear and tear issues present ongoing challenges for rotary aviation apex seals, as the dynamic nature of engine operation leads to inevitable degradation over time. Factors such as friction, thermal cycling, and mechanical stress contribute to wear and tear on apex seals, necessitating routine maintenance and inspection to identify and address potential issues. Mitigating wear and tear issues is crucial in preserving the efficiency and longevity of apex seals, ensuring uninterrupted engine performance and reliability.
Design and Functionality of Rotary Aviation Apex Seals
In this section, we delve into the critical aspects of Design and Functionality of Rotary Aviation Apex Seals. Rotatory aviation apex seals are pivotal components that greatly influence engine performance. The design of these seals plays a significant role in ensuring optimal engine functionality and efficiency. By understanding the intricate details of apex seal design, engineers can fine-tune rotary aircraft engines for maximum output and reliability.
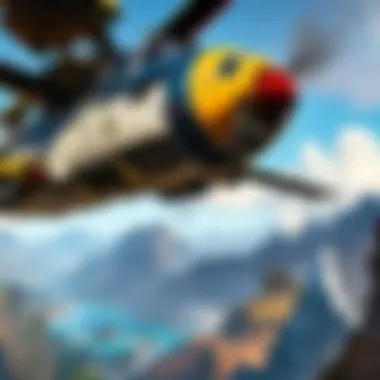
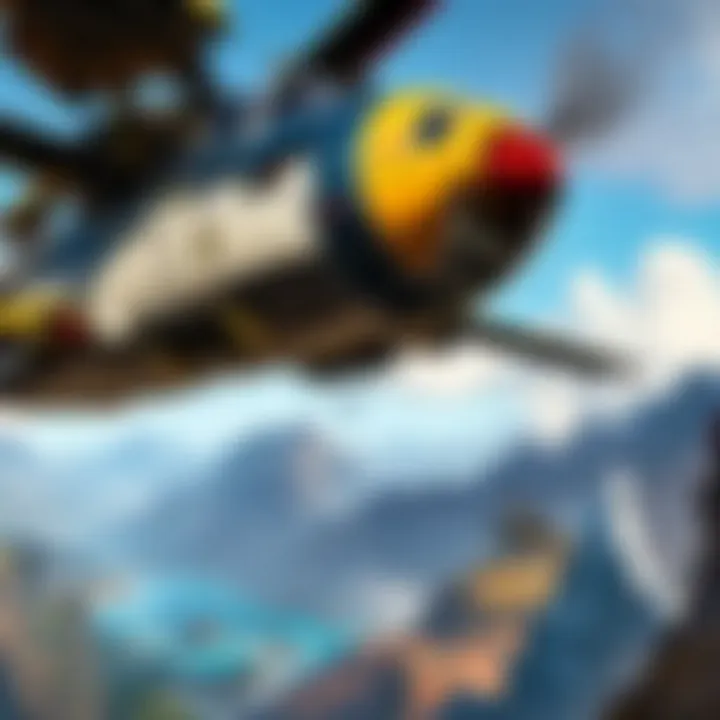
Materials Used in Apex Seal Construction
High-Temperature Alloys
High-temperature alloys are a fundamental choice in rotary aviation apex seal construction due to their exceptional heat resistance properties. These alloys can withstand the extreme temperatures and pressures within rotary engines, ensuring longevity and durability. Their unique characteristic lies in their ability to maintain structural integrity under high thermal stress, making them a popular choice for enhancing rotary engine performance. While high-temperature alloys offer superb heat resistance, they may be prone to higher production costs compared to other materials, a factor that engineers must consider in apex seal design.
Carbon-Based Composites
Carbon-based composites are another crucial material used in apex seal construction, known for their lightweight yet robust nature. These composites provide an excellent balance between strength and weight, contributing to improved engine efficiency. Their key characteristic lies in their high strength-to-weight ratio, making them a beneficial choice for enhancing rotary aviation apex seals. However, carbon-based composites may have limitations in terms of heat resistance compared to high-temperature alloys, requiring careful consideration in specific engine configurations.
Seal Geometry and Engine Performance
Apex Seal Profiles
The geometry of apex seal profiles plays a significant role in determining engine performance in rotary aircraft. Different profiles can impact compression ratios, combustion efficiency, and overall engine output. Engineers carefully design apex seal profiles to ensure proper sealing and minimal leakage, optimizing engine function. The unique feature of apex seal profiles lies in their ability to maintain airtight seals within the combustion chamber, which is crucial for maximizing engine power. However, intricate profiles can sometimes lead to increased friction and wear, requiring meticulous maintenance.
Sealing Mechanisms
Sealing mechanisms are vital components that ensure effective engine operation by preventing gas leakage and maintaining combustion pressure. The key characteristic of sealing mechanisms is their ability to create airtight barriers within the engine, promoting optimal combustion efficiency. Engineers favor sealing mechanisms that offer both tight seals and minimal friction, balancing performance and durability. However, the complexity of sealing mechanisms can sometimes introduce challenges in terms of maintenance and troubleshooting, requiring skilled inspection and lubrication practices.
Impact of Apex Seal Design on Engine Efficiency
Compression Ratios
Compression ratios play a crucial role in determining engine efficiency and power output in rotary aviation systems. Optimal compression ratios can enhance combustion efficiency and overall engine performance. The key characteristic of compression ratios is their ability to compress air-fuel mixtures effectively, maximizing energy conversion. Engineers focus on optimizing compression ratios to achieve the desired balance between power and fuel consumption. However, improper compression ratios can lead to engine knocking and decreased efficiency, highlighting the importance of precision in apex seal design.
Combustion Chamber Dynamics
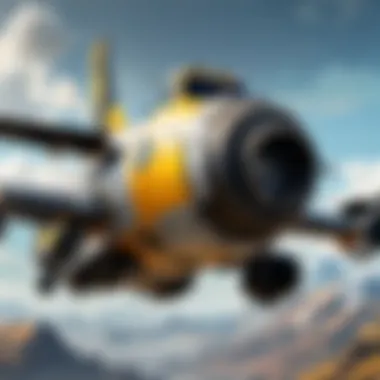
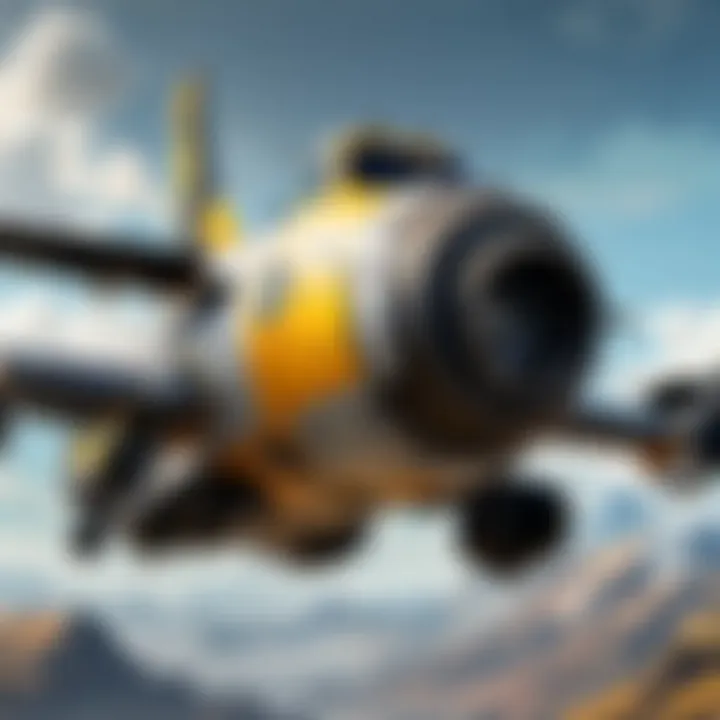
Combustion chamber dynamics significantly impact engine performance by influencing airflow, fuel combustion, and exhaust emissions. Understanding the dynamics of the combustion chamber is essential for optimizing rotary aviation engine efficiency. The key characteristic of combustion chamber dynamics lies in their ability to promote efficient fuel burning and energy release, directly impacting power output. Engineers continuously refine combustion chamber designs to enhance turbulence, mixing, and heat distribution, aiming to achieve peak engine performance. However, complex dynamics may introduce challenges in balancing performance with emissions control, necessitating advanced engine tuning and maintenance practices.
Maintenance and Optimization of Rotary Aviation Apex Seals
In delving into Maintenance and Optimization of Rotary Aviation Apex Seals within this extensive document, the pivotal significance of ensuring the longevity and efficiency of these seals in rotary aircraft engines comes to the forefront. The meticulous care and fine-tuning required for apex seals play a critical role in maintaining peak engine performance and reliability. By focusing on the specific elements, benefits, and considerations surrounding the Maintenance and Optimization of Rotary Aviation Apex Seals, a comprehensive understanding of the complexities involved in preserving and enhancing engine functionality is achieved.
Routine Inspection and Lubrication Practices
- ** Preventative Maintenance Strategies:** The adoption of Preventative Maintenance Strategies stands as a cornerstone in the realm of rotary aviation apex seals upkeep. These strategies offer a proactive approach to identifying and addressing potential issues before they escalate, thereby safeguarding the overall operational efficiency of rotary engines. The key characteristics of Preventative Maintenance Strategies lie in their ability to prevent unexpected breakdowns and reduce the likelihood of costly repairs, making them a prudent choice in the context of optimizing engine performance. The unique feature of these strategies lies in their ability to enhance the longevity and functionality of apex seals while minimizing downtime, highlighting their advantageous implications in ensuring the seamless operation of rotary engines.
- ** Lubricant Selection Criteria:** The selection of appropriate lubricants holds immense importance in the maintenance and optimization of rotary aviation apex seals. Lubricant Selection Criteria emphasize the compatibility of lubricants with the seal materials, ensuring proper functionality and minimizing wear over time. The key characteristic of these criteria lies in their ability to provide optimal lubrication under high-temperature and high-pressure conditions, crucial for the prolonged durability of apex seals. The unique feature of adhering to specific Lubricant Selection Criteria is the enhanced sealing efficiency and reduced frictional losses, translating into improved engine performance and longevity in the context of this article.
Future Developments and Innovations in Rotary Aviation Apex Seals
In this section, we delve into the future trajectory of rotary aviation apex seals, foreseeing the advancements that will shape engine performance. The evolution and enhancement of apex seals in rotary aviation engines are vital for pushing the boundaries of efficiency and reliability. Understanding the upcoming innovations is key to staying at the forefront of aviation technology.
Emerging Technologies and Research Trends
Nano-Coating Applications:
Nano-coating applications represent a groundbreaking advancement in seal technology, offering unparalleled protection and longevity. The key characteristic of nano-coatings lies in their molecular-scale thickness, providing a microscopic shield against wear and corrosion. Nano-coatings are a popular choice in this article due to their ability to enhance seal durability without compromising performance. The unique feature of nano-coating applications is their ability to self-heal, ensuring continuous protection against abrasive forces. While nano-coatings bring outstanding benefits to rotary aviation apex seals, their application may involve complex processes that require specialized expertise.
Advanced Seal Materials:
The utilization of advanced seal materials signifies a monumental leap in improving rotary aviation apex seals. The standout feature of advanced seal materials is their exceptional heat and wear resistance, essential for withstanding the extreme conditions within rotary engines. Opting for advanced seal materials is a beneficial choice for this article as it underlines a commitment to optimizing engine performance and longevity. The unparalleled feature of advanced seal materials lies in their ability to maintain structural integrity under immense pressure, ensuring minimal degradation over time. Despite their numerous advantages, advanced seal materials may come with a higher price point, necessitating careful cost-benefit analysis for integration into existing engine systems.
Environmental Considerations and Sustainability
Efficiency Improvements:
Efficiency improvements in rotary aviation apex seals play a pivotal role in elevating overall engine performance. The key characteristic of efficiency improvements lies in their capacity to optimize fuel consumption and power output, enhancing the operational efficiency of rotary engines. Incorporating efficiency improvements is a beneficial choice for this article as it aligns with the pursuit of sustainable aviation practices. The unique feature of efficiency improvements is their ability to streamline combustion processes, reducing energy wastage and enhancing overall engine efficiency. However, implementing efficiency improvements may require meticulous calibration and fine-tuning to achieve optimal results.
Reduced Emissions Impact:
The emphasis on reducing emissions impact through rotary aviation apex seals signifies a momentous shift towards environmental sustainability. The key characteristic of reduced emissions impact initiatives is their focus on minimizing engine exhaust pollutants, contributing to cleaner air quality. Choosing to address reduced emissions impact is a beneficial choice for this article as it highlights a commitment to mitigating aviation's environmental footprint. The unique feature of reduced emissions impact strategies is their integration of exhaust gas recirculation mechanisms, effectively lowering harmful emissions without compromising engine performance. While reducing emissions impact brings significant advantages, it may necessitate investment in specialized emission control systems to ensure compliance with stringent environmental regulations.